CNC Machining has transformed manufacturing, offering a precise and efficient way to make parts and other components for a wide array of industries. This advanced technology uses machines controlled by computers for cutting, drilling, milling, and other operations on various substances like metals, plastics, as well as wood. The precision that can be achieved through CNC cutting is unmatched, allowing for complex design to be completed with extreme accuracy. By replacing manual intervention with automation, CNC machines have significantly reduced the likelihood of human error and increased the speed of production. The combination of precision and efficiency has helped make CNC machine machining an integral component of the modern manufacturing process.
One of the main advantages of CNC machining is its unparalleled precision, and the ability to make intricate designs. Unlike manual machining, where the operator controls the machine, CNC machines follow specific instructions that cut, shape, and form the materials with astonishing precision. It reduces the possibility of error by a significant amount, and allows for production of components which meet exact specifications. The most intricate geometries and detail, and precise tolerances are achievable by CNC manufacturing, making it the ideal tool for businesses where there is a need for high levels in precision, for instance aerospace, where even tiny mistakes in parts could result in serious effects.
Efficiency of CNC machining is another key factor in its widespread adoption. Traditional machining methods require highly skilled workers to operate the machinery, adjust settings, and then change the machines for each job. The process is not just labor-intensive, but it is also susceptible to human errors. CNC machining on the side, however, allows for the automation of these tasks, allowing machines to work continuously under very little oversight. After a program has been set and the machine has been supplied with the necessary material, it can perform multiple actions without interruption, significantly shortening the production process. CNC machines can also be capable operating continuously, which makes them perfect for big production runs. This level of efficiency enables manufacturers to meet tight deadlines, boost their production and cut down on labor expenses in the process, while still maintaining top quality standards.
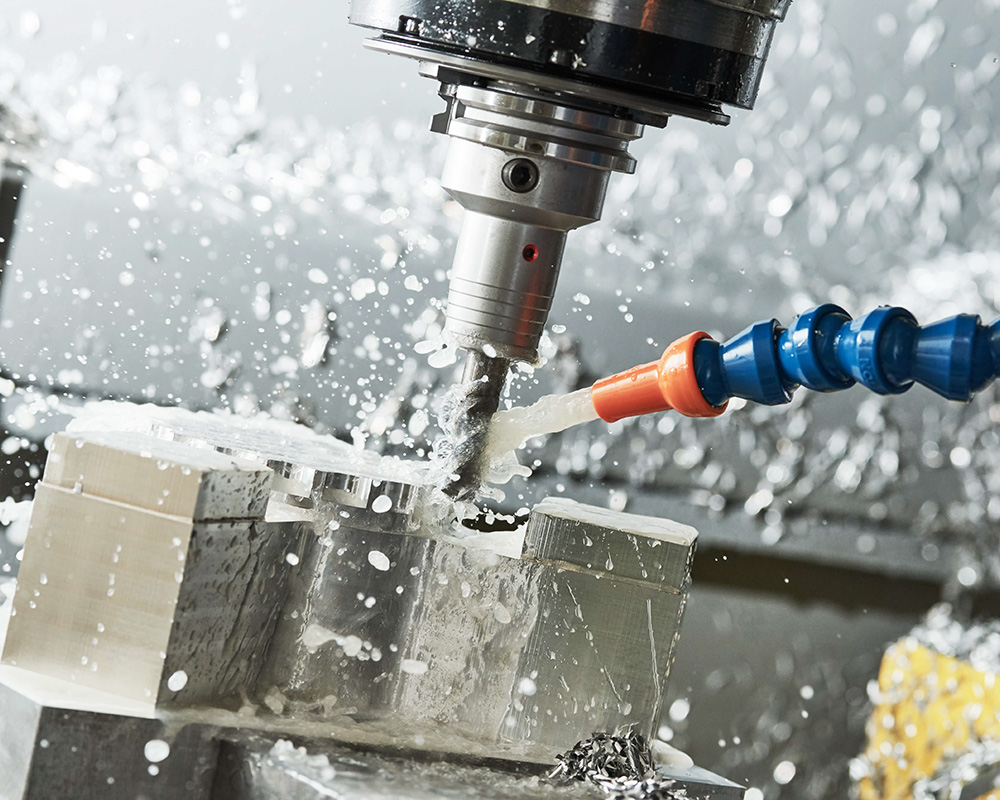
Also, CNC parts offers high reliability, which means that every component produced is exactly like the original design. This is essential in the industries that demand mass production of standardized components like automotive or consumer electronics. Since CNC machines adhere to programmed procedures, they can make hundreds or even thousands of parts with minimal variations in the quality. This ensures the durability of the finished products but also reduces loss, since fewer pieces are rejected due to defects. Additionally, since the designs created by CNC machining can be easily altered or upgraded, companies can swiftly adjust to changes in product specifications or demands of customers without the expense of Retooling or recalibration of the machine.
Although it has many benefits, CNC machining is not without its difficulties. The biggest obstacle that many businesses face, particularly small and medium-sized firms in the beginning is the investment necessary. CNC machines can be more costly as compared to traditional machining tools in addition to an expense for specialized software, maintenance, and operator instruction to think about. However, the advantages over the long term such as reduced labor costs, faster production cycles, and increased quality of parts – often justify the initial investment. Furthermore, the rise of CNC manufacturing service providers has allowed firms that don’t have enough capital to put into their machines to still take advantage of the latest technology. They can create special parts as needed, offering a cost-effective solution for firms that require high-quality manufacturing without the initial costs.
Future of CNC machining is bright, as technological advancements continue pushing the boundaries of what these machines can attain. With CNC machines becoming more sophisticated, they’re increasingly integrated with other technologies like 3D printing and robotics, to create hybrid manufacturing processes that combine the strengths of a variety of techniques. Furthermore, the rise of smart manufacturing as well as the Industrial Internet of Things (IIoT) allows for greater connectivity and automation in CNC machining, allowing the machines to interact with each other and adjust operations in real time based on the data from sensors. While these advancements continue to evolve, CNC machining will remain a vital tool in the development of modern manufacturing, providing even greater precision as well as speed and flexibility for future generations of products.
Leave a Reply